Charged EVs | FEV explores die-casting alternative for body-in-white design
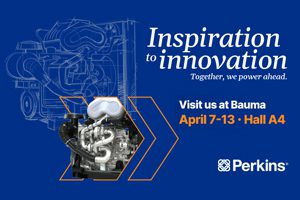
Automotive and industrial equipment manufacturer FEV is working with 18 global partners from the automotive and metal industries in the MeGiCast consortium project to investigate the potential of gigacasting (large-scale die-casting) for more efficient vehicle body production.
Aluminum die casting of entire modules allows for efficient production and reduces development and production times. FEV is taking this approach one step further and developing highly integrated body designs with the aim of reducing costs, weight and carbon emissions.
The MeGiCast consortium partners are analyzing a front section in gigacasting design and comparing it with a modern multi-material approach. The applied hybrid manufacturing technologies could achieve weight savings of up to 18%.
FEV has developed a hybrid manufacturing technique that uses large sheet metal components for flat structures and applies reinforcements using the casting process. This creates a front part made from three components up to 18% lighter than a variant based on gigacasting alone.
The reduction in component weight offers advantages but also poses challenges because of the complexity of the cast parts, high investment costs, production requirements and questions regarding service life, according to FEV.
“FEV is working on integrated design approaches that take into account customer-relevant safety and quality requirements as well as production-related aspects,” said Christian Kürten, Managing Director of FEV Vehicle. “These include simplified assembly, a reduced number of variants and an optimized cost structure in production.”
Source: FEV
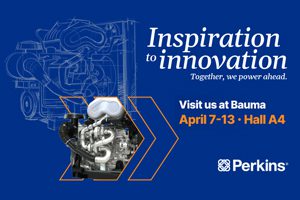